Technical Specifications of Custom OLED Panels in the Display Industry
Technical Specifications of Custom OLED Panels in the Display Industry
In the rapidly advancing display industry, custom OLED (Organic Light - Emitting Diode) panels have emerged as a key solution, enabling tailored display experiences across diverse applications. Unlike standard panels, custom OLED panels are designed to meet specific requirements in terms of size, shape, performance, and functionality. Understanding the technical specifications of these panels is essential for manufacturers, designers, and end - users looking to leverage the unique capabilities of OLED technology. This article delves into the critical technical aspects of custom OLED panels, optimized for Google SEO to enhance visibility and provide in - depth industry - relevant insights.
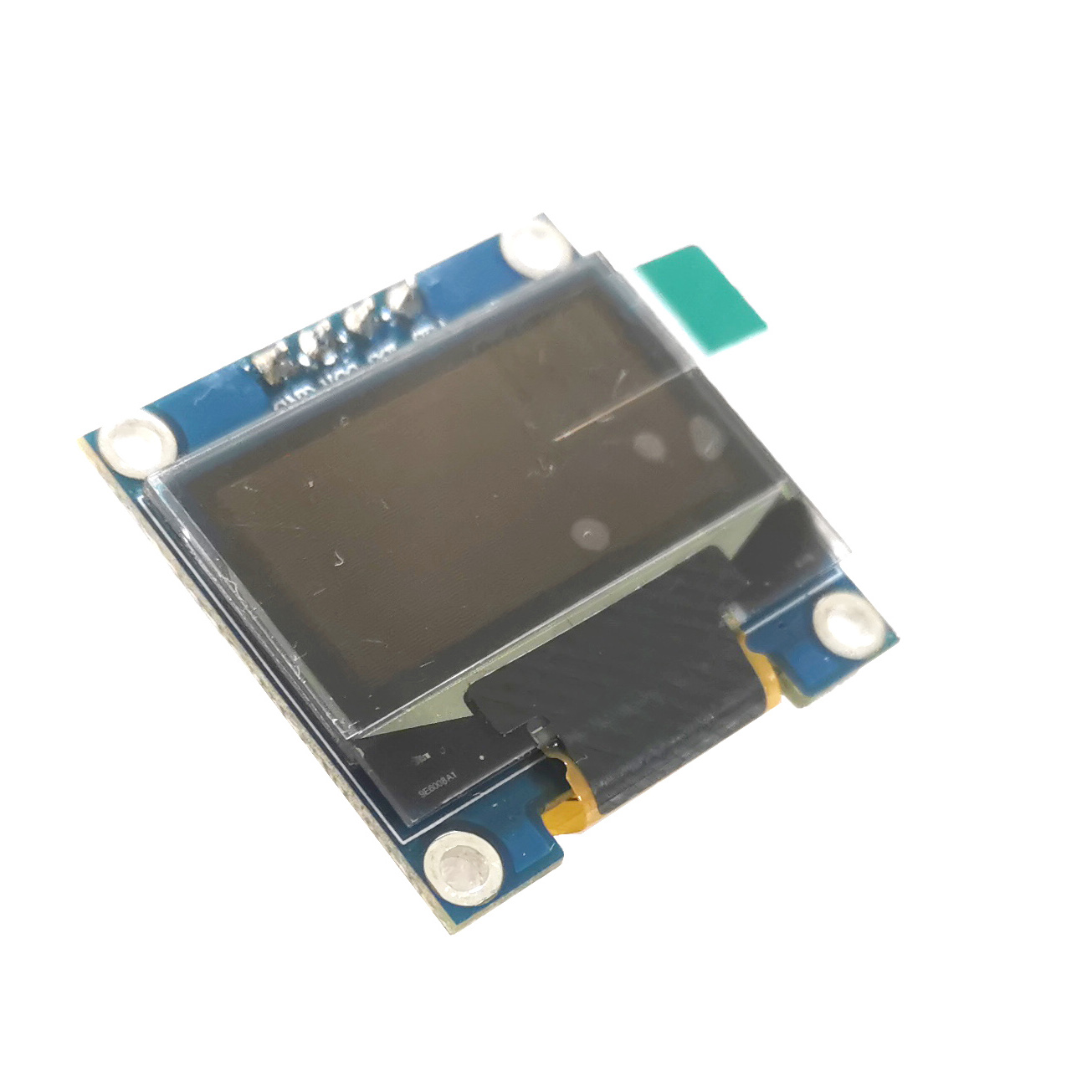
1. Display Structure and Basic Principles
Custom OLED panels operate on the self - emissive principle of organic materials. Each pixel within the panel consists of organic thin - film layers sandwiched between two electrodes. When an electric current passes through these layers, the organic materials emit light, eliminating the need for a backlight, a characteristic that sets OLEDs apart from traditional LCD panels. This self - emissive nature offers several advantages, including high contrast ratios, fast response times, and wide viewing angles.
- Pixel Architecture: The pixel arrangement in custom OLED panels can be customized based on the application. For example, in high - resolution displays for professional graphic design, a fine - pitch pixel layout is crucial. Advanced manufacturing techniques such as shadow masking or inkjet printing are employed to ensure precise pixel placement, with a pixel pitch tolerance often controlled within ±0.003mm for high - end custom panels.
- Substrate Selection: Custom OLED panels can utilize different substrate materials. Glass substrates are commonly chosen for applications that require high rigidity and flatness, such as large - format digital signage or industrial control panels. On the other hand, flexible plastic substrates, like polyimide, enable the creation of bendable or rollable OLED panels, opening up possibilities for wearable devices, curved displays, and flexible electronics. The choice of substrate impacts factors such as panel durability, weight, and form factor flexibility.
2. Material Specifications
2.1 Organic Materials
The organic materials used in custom OLED panels are the core of their light - emitting function, and their selection can be tailored to specific performance requirements.
- Small - Molecule Organic Materials: Materials such as tris(8 - hydroxyquinoline)aluminum (Alq3) are known for their high luminous efficiency and excellent color purity. They are typically deposited onto the substrate through vacuum thermal evaporation, allowing for the formation of a uniform and thin layer with a thickness precision of ±0.1nm. Small - molecule materials are often preferred in custom panels where accurate color reproduction and high brightness are essential, such as in professional photography monitors or high - end gaming displays.
- Polymer Organic Materials: Polymer - based organic materials, like poly(phenylene vinylene) (PPV), offer the advantage of ease of processing, usually via solution - based methods such as spin - coating or inkjet printing. This makes them suitable for large - area custom OLED production, reducing costs and increasing production efficiency. While their luminous efficiency and color stability may be slightly lower compared to small - molecule materials, they are commonly used in consumer - grade custom panels, such as affordable smartwatches or digital photo frames.
2.2 Electrodes
The electrodes in custom OLED panels play a vital role in conducting electricity to the organic layers, and their properties can be optimized for specific applications.
- Anode: Indium tin oxide (ITO) is a widely used anode material due to its high transparency and electrical conductivity. For custom panels, the sheet resistance of the ITO anode is typically required to be ≤10 Ω/sq to ensure efficient current flow. In some cases, especially for flexible custom OLEDs, alternative transparent conductive materials like graphene or silver nanowires are being explored to overcome the brittleness of ITO.
- Cathode: Metals with low work functions, such as calcium or magnesium, are often used as cathodes, combined with a thin layer of a metal oxide or fluoride to enhance electron injection. The thickness of the cathode layer is carefully controlled, usually within 10 - 50nm, to balance electrical performance and optical transparency.
3. Display Performance Specifications
3.1 Resolution and Pixel Density
Custom OLED panels can be designed with a wide range of resolutions to meet different application needs.
- Resolution Options: Resolutions can vary from low - resolution for simple signage applications to ultra - high - definition (UHD) or even higher for professional and high - end consumer products. For example, a custom OLED panel for a virtual reality headset might require a high - resolution display to provide a immersive visual experience, while a custom panel for a simple digital clock could have a lower resolution.
- Pixel Density: Pixel density, measured in pixels per inch (PPI), is a critical factor in determining the sharpness of the display. For consumer - grade custom OLED panels, a PPI of 300 - 400 is often considered standard, providing a clear and detailed visual experience. In professional applications, such as medical imaging or graphic design, custom panels with a PPI of 500 or more are preferred to display fine details accurately.
3.2 Brightness and Contrast
- Brightness: The brightness of custom OLED panels is measured in nits (cd/m²) and can be customized based on the application environment. Indoor - use custom panels typically have a brightness range of 200 - 500 nits, which is sufficient for normal ambient lighting conditions. For outdoor - facing applications, such as digital billboards or outdoor signage, custom OLED panels with higher brightness levels, often 1000 nits or more, are required to ensure visibility in direct sunlight.
- Contrast: One of the key advantages of OLED technology is its ability to achieve an almost infinite contrast ratio. Since each pixel can be completely turned off, resulting in true black levels, custom OLED panels offer vivid and immersive visual experiences with deep blacks and bright whites, enhancing the overall image quality.
3.3 Color Accuracy and Gamut
- Color Accuracy: Color accuracy is crucial for applications where true - to - life color representation is required. Custom OLED panels use metrics such as Delta E (ΔE) to measure color accuracy. A lower ΔE value indicates more accurate color reproduction. For professional - grade custom panels, a ΔE < 2 is considered excellent, ensuring that colors on the display closely match the original content. In consumer - grade custom products, a ΔE < 5 is generally acceptable for a satisfactory viewing experience.
- Color Gamut: Custom OLED panels can cover a wide color gamut, often exceeding the sRGB standard. High - end custom models may cover a significant portion of the DCI - P3 or Adobe RGB color spaces, providing a rich and diverse range of colors. This wide color gamut is particularly beneficial for applications such as video production, gaming, and digital art.
3.4 Response Time
4. Electrical Specifications
4.1 Power Consumption
Power consumption in custom OLED panels depends on multiple factors, including panel size, resolution, brightness level, and the content being displayed. Since OLEDs are self - emissive and can turn off individual pixels, they consume less power when displaying dark content compared to bright content.
- Typical Consumption: For a medium - sized (e.g., 5 - 6 inches) custom OLED panel with a 1080×1080 resolution, the power consumption at 50% brightness may range from 1 - 3W. As the brightness increases or the resolution goes up, power consumption also rises accordingly. Manufacturers often provide power consumption data under different operating scenarios to help users understand the energy requirements of their custom OLED products.
4.2 Driving Voltage and Current
- Driving Voltage: The driving voltage for custom OLED panels is relatively low, usually in the range of 3 - 10 volts. Precise control of the driving voltage is essential to ensure consistent pixel performance and prevent issues such as pixel burnout or uneven brightness. Customization of the driving voltage can be adjusted based on the specific design and requirements of the panel.
- Driving Current: The driving current is carefully regulated to control the light emission of each pixel. The current density is typically in the range of 1 - 10 mA/cm², and accurate current control is crucial for maintaining color consistency and display longevity. Different custom applications may require fine - tuning of the driving current to optimize performance.
5. Mechanical and Environmental Specifications
5.1 Size and Shape
- Size Customization: Custom OLED panels can be produced in a wide variety of sizes, ranging from small, wearable - friendly dimensions to large - format panels for commercial applications. The size of the panel is determined by the specific needs of the application, with small sizes suitable for smartwatches, ear - worn devices, or embedded systems, and large sizes ideal for digital signage, video walls, or immersive display installations.
- Shape Customization: One of the unique features of custom OLED panels is the ability to customize the shape. Panels can be cut or manufactured into irregular shapes, circular, or other non - rectangular forms to fit specific design requirements. This shape customization is highly valued in applications such as interior design, automotive dashboards, and consumer electronics with innovative form factors.
5.2 Durability and Environmental Resistance
- Durability: Due to the thin and organic nature of their components, custom OLED panels are generally more fragile than traditional LCD panels. However, with proper encapsulation and protective layers, their durability can be enhanced. Encapsulation techniques, such as thin - film encapsulation (TFE) or glass encapsulation, are used to protect the organic layers from moisture and oxygen, which can degrade the display over time.
- Environmental Resistance: Custom OLED panels can operate within a certain temperature and humidity range. Typically, they can function in temperatures ranging from - 20°C to 60°C and relative humidity levels of 10% - 90%. However, extreme environmental conditions can still affect their performance and lifespan. For outdoor or harsh - environment applications, additional protective measures and environmental conditioning may be required.
6. Connectivity and Interface Specifications
6.1 Video Inputs
Custom OLED panels require video input ports to connect to various devices, and the choice of interfaces can be customized based on the application.
- Common Interfaces: HDMI (High - Definition Multimedia Interface) is a widely used video input interface for custom OLED panels, supporting high - definition video and audio transmission. DisplayPort is also becoming increasingly popular, especially for high - resolution and high - refresh - rate custom panels, as it offers higher bandwidth. USB - C, with its versatility in supporting video, data, and power delivery, is another emerging interface that provides seamless connectivity with modern devices
6.2 Control and Communication Interfaces
- Serial and Ethernet Interfaces: For applications where remote control or integration into a larger system is required, serial interfaces such as RS - 232 or RS - 485, and Ethernet interfaces are commonly used. These interfaces allow for the transmission of control commands, settings, and status information, enabling precise management of the custom OLED panel.
- Wireless Interfaces: Some custom OLED panels also support wireless communication technologies such as Wi - Fi or Bluetooth. This enables wireless connection to mobile devices or control systems, providing greater flexibility in setup and operation, especially for applications like smart home displays, portable devices, or interactive installations.
7. Industry Applications and Technical Specification Considerations
7.1 Consumer Electronics
In the consumer electronics industry, custom OLED panels are used in a wide range of products. In smartphones, custom panels can be designed to fit unique form factors, offer high - resolution displays for immersive gaming and media consumption, and have low power consumption for extended battery life. Smartwatches often feature custom OLED panels with small sizes, high pixel densities, and good color accuracy for clear and vibrant visual displays on the wrist. Digital photo frames may use custom OLED panels with large sizes, high brightness, and wide color gamuts to showcase photos in the best possible way.
7.2 Digital Signage and Advertising
For digital signage and advertising, custom OLED panels provide unique advantages. Large - format custom OLED panels with high brightness, excellent contrast, and wide color gamuts are ideal for creating eye - catching displays in shopping malls, airports, and other public spaces. The ability to customize the size and shape of the panels allows for creative and immersive digital signage installations that can attract and engage audiences effectively.
7.3 Automotive
In the automotive industry, custom OLED panels are increasingly used for dashboard displays, center console screens, and ambient lighting. Custom panels can be shaped to fit the interior design of the vehicle, offering high - resolution displays for important information such as speed, navigation, and vehicle status. The fast response time and high contrast of OLED panels ensure clear visibility under different lighting conditions, enhancing driver safety and the overall driving experience.
7.4 Medical and Healthcare
In medical and healthcare applications, custom OLED panels are used for diagnostic displays, surgical monitors, and patient information terminals. High color accuracy and resolution are crucial for accurately displaying medical images and data. Custom panels can be designed to meet specific medical standards and requirements, such as being compatible with medical equipment, having anti - glare coatings for better visibility in clinical environments, and being easy to clean and disinfect.
In conclusion, custom OLED panels offer a high degree of flexibility and customization in the display industry, catering to a diverse range of applications. By understanding and carefully specifying their technical aspects, manufacturers can create innovative and high - quality products, while users can select the most suitable custom OLED panels for their specific needs. With continuous technological advancements, custom OLED panels are expected to play an even more significant role in the future of the display industry. Incorporating relevant keywords and following SEO best practices, this article aims to enhance the visibility of information related to custom OLED panels, facilitating knowledge sharing and promoting the development of this exciting display technology.